Installation Instructions
For products by
The Copperworks of Don Miller, and other expert installations.
A photo alternative with differing methods is here.
Table of Contents
Safety
Ladder Accessories
An item that should be mandatory for all ladders is adjustable swivel feet. The main purpose of these feet is to adjust to uneven ground surfaces. The second purpose of these feet is that the ball joint type swivel pads provide excellent traction on uneven surfaces. These feet are called XTENDA LEG TM, and might be found at a painters supply store.
Also very useful in some situations is a special ladder jack that allows the ladder to rest against the roof surface, and allows a large enough gap between the edge of the roof and the ladder to pass the gutter through. The ladder jack might also work while leaned against the wall where the eave does not extend past the span of the ladder jack. It is important for stability that the ladder jack has a broad span of several times the ladder width between the ladder jack legs.
Scaffolding
Be prepared to use properly installed scaffolding where it will improve safety or the ease of installation.
Fall Arrestors
Some companies produce fall arrestors for use with ladders, and other fall arrestors for other locations such as on the top of roofs and scaffolding. The unit mounts to a secure location, and a spring loaded cable attaches to the worker. If the cable pulls out too quickly, the arrestor locks up.
Aros Inc. - 883 South 200 East, Salt Lake City, UT 84111 (801)531-9279, fax 9966, http://safety.aros.net
Miller / Dalloz - 1355 15th St., Franklin, PA 16323 (814)432-2118, fax 2415 www.cdalloz.com
Climbing Equipment
Sports climbing equipment can sometimes offer a vital safety backup system, or may provide a sole means of support in daring situations on rooftops.
Some basic climbing equipment which might be useful to an installer might be a harness, 100 feet or more of high quality perlon, a pair of Jumars (tm), and stirrups, 4 locking steel D shaped carabineers, and several 4 foot loops of webbing.
Climbing equipment should be carefully inspected before each use. Nylon is subject to degradation from excessive ultraviolet exposure, heat, and chemicals such as the acid in animal urine which can cause a 50% loss in strength with no visible damage. The carabineers should be of steel rather that the more common aluminum, because aluminum carabineers can develop invisible cracks over time, in an abusive environment, and have been known to fail without warning. (These cautions are garnered from scientific testing and real incidents from within the organized sport of hang gliding, and form part of their safety standards. www.ushga.org)
Fire Safety
Always keep a fire extinguisher at hand at your work site. Keep flammables away from the soldering furnace. Don’t leave a lit soldering furnace unattended. Keep soldering equipment in a well-ventilated environment. Solder occasionally splatters explosively. Always use eye protection while soldering.
Delicate Roofs
Some installation requires working and putting ladders on delicate roof surfaces such as Spanish tile and slate. It is good business for a contractor to consider this factor before entering into an agreement with the property owner, and to discuss how matter such as broken tiles will be dealt with. Sometimes one might photograph and document broken tiles before and after a contract, especially if other trades are concurrently working on the roof, in order to help delegate responsibility in the event of damage to the roof surface.
One should always have a strategy for walking on a particular roof surface. On Spanish tiles it is best to distribute the weight of each foot onto two tiles, with the toe on the center of one tile, and the heel on the center of the next one. Avoid stepping on tiles that are on the edge of the field and on hips and ridges.
One method that works well with many delicate roof situations is having a number of burlap bags loosely filled with wood chips, to distribute the load and avoid cracking tiles. Wood planks can be set on these bags, on which ladders with adjustable legs might also be secured. The wood planks might also be secured from sliding off of the roof in some manner
Planning
Following is a most important reference book for the raingutter installer. Most contractors’ size raingutters and downspouts based on experience of what works or doesn’t work in a particular region, however it is a good idea for the professional installer to have some solid math based sizing formulas to follow.
Architectural Sheet Metal Manual - (ASMM)
By the Sheet Metal and Air Conditioning Contractor’s National Association, Inc. (SMACNA)
4201 Lafayette Center Drive, Chantilly, VA 22021
(703) 803-2989 begin_of_the_skype_highlighting (703) 803-2989 end_of_the_skype_highlighting, www.smacna.org
Downspout Location
One of the first considerations in raingutter planning is downspout placement, which is largely an aesthetic consideration. In any given desired downspout location, there is a good chance that the location will work for the following reasons:
A) The roofline may be sloping towards the desired downspout location - Good.
B) The roofline may be level towards the desired downspout location - OK, perhaps.
C) The roofline may be sloping away from the desired downspout location, but perhaps the region is hot and dry, so that any standing water will dry fast, and maybe the roof area drained is small.
D) The roofline may be sloping away from the desired downspout location, but there is enough space on the fascia and esthetic considerations make sloping the gutter downward in relation to the roofline acceptable, or if the raingutter large enough, it may be possible to solder a second bottom into the raingutter to force the water to flow towards the downspout. (See instructions on this option later)
Having a little pitch to the gutter might slightly reduce the buildup of dirt and ice, but it is seldom practical or necessary; what is essential is that the gutter be able to dry out in a day or so, to reduce corrosion and to prevent the breeding of mosquitoes. Keeping a galvanized-steel gutter dry is key to its longevity; in a copper gutter, dryness is not as critical.
There is usually no way that a person can say which way a roofline is sloping by simply looking at it. Illusion will always predominate. The most practical way to determine pitch of a long or complex roofline is with a water-level. The results of a water-level survey might affect decisions about downspout placement.
How to make and use a Water-Level
There are various water levels available at hardware stores, but Don Miller found (during his contracting years) that his self-made water-level worked better than commercially available models. Don’s water-level with a reservoir and thin tubing has the advantage that a little water lost, or a little expansion or contraction in the tubing that occurs when the tubing drapes down to various heights, makes no significant change in the level of the water.
The reservoir on the water-level is a discarded disposable plastic I.V. plasma bottle with a large hole cut in the top. Attach to the IV bottle 100 feet of 1/4” clear flexible poly-tubing like that used as air tube in aquariums. At the other end of the tubing attach a brass aquarium valve.
Hang the reservoir filled with water in any convenient location near, but a little below, the level that you will be measuring. If the water has air dissolved into it, give plenty of time for all of the air bubbles to disappear. Set the other end of the tube down in a low area and open the valve. Be sure that absolutely every air bubble is expelled, and then close the valve. Carry the valve end of the tube up to several inches higher than the reservoir level and open the valve. Hold the valve to a point on the roofline that you wish to reference to, and with a marker, make a mark on the tube below the valve, of the level of the water in the tube.
For accuracy it is important to be patient with this small diameter tube and be sure that the level of the water has stopped changing. The first location is a reference point as you go around the fascia and measure how far any particular point is above or below the mark on the tube, and the reference point first measured.
In terms of installing Copperworks bronze brackets, here is a simple example. You may choose to make your first reference point at a location on the fascia furthest from a desired downspout location, and using one bracket held in its highest possible position, make a mark where the lag screw will need to penetrate the fascia. You could then find the same level position on the fascia where the desired downspout location will be, and figure out where a bracket would be positioned at that location for adequate flow, and chalk a line between the two points along which 3/16” diameter holes will be predrilled for the bracket lag screws.
Allow for Expansion and Contraction
A general formula for the rate of expansion and contraction of a copper gutter (in relation to some expansion also factored into the structure) is 1/8 inch per 10 lineal feet copper gutter per 100 degrees farenheight Fahrenheit temperature change. The gutter will lengthen as the temperature rises and shrink as the temperature drops. The temperature at the time of installation needs to be taken into account, as well as the highest and lowest expected temperatures. Be sure to allow for expansion seams in strategic locations along long straight lengths as detailed in the Architectural Sheet Metal Manual. The location of expansion seams may affect downspout placement.
Raingutters installed with Copperworks bronze brackets deal with expansion and contraction well. The back of the gutter is not fastened to the bracket, but can slide in the hook. The bracket can move back and forth somewhat at the front where the gutter is attached, and there is a 3/8” gap between the raingutter back and the fascia where the gutter goes around corners.
Galvanic Corrosion
Copper is at the top of the galvanic scale. Other metals, such as steel, aluminum, and zinc will corrode more quickly when in contact with copper or the flow from a copper pipe. Bronze, brass, some alloys of stainless steel and nickel are compatible with copper. If the copper is contacting a very thick piece of steel or iron in a dry location, the effect on the steel or iron may be negligible. If the surface of the other metal is large and the surface of the copper is small, the effect on the other metal may be negligible. If a copper gutter is being slipped behind a steel flashing, separate the metals electrically, and maybe the flashing will be OK until it is time to reroof. If a large surface of copper is contacting a small surface of the other metal, or if water drops from a copper surface onto the surface of another metal, the other metal may not last long. Be sure that all fasteners for a copper raingutter do not contain any mild steel. If it sticks to a magnet, then it has no place in a copper gutter system.
Installation
Bronze Gutter Bracket Installation
Gutter brackets should be not more than 36 inches apart. This 36 inch maximum spacing of gutter fasteners (brackets) is a standard that is recommended in various publications on the subject, and for various reasons. If the brackets were spaced farther apart, say 48 inches, the raingutter and brackets might still be able to support the weight of being full of water, but one may not be able to lean a ladder against the gutter without damaging it. In freezing areas, where the gutter is subject to ice loads from the roof, brackets are often placed closer to 24 inches apart.
The fascia or row of rafter tails should be fairly well aligned laterally, and be of a consistent vertical angle. Any bracket attachment point that is more than 1/4 inch out of alignment with its nearby attachment points must be adjusted in some manner.
Chalk a line on the fascia or rafter tails on which to drill the holes for the gutter bracket screws. Predrill the lag screw holes with a 3/16” by 12 inch extension drill bit before installing the lag screws.
If the brackets are being attached to masonry or stone, then lead caulk-in anchors and 1/4” stainless steel machine screws are used to bolt the brackets to the anchors.
Bolt the brackets to the surface with the lag screws.
The 1/4 inch lag screws should NOT be tightened snug! It should be tightened until the head of the screw just contacts the bracket, and the bracket is flush against the mounting surface, but the bracket retains some flexibility.
There are several reasons for this. 1) So that the bracket may be moved slightly to help with gutter to bracket fastener installation. 2) Gutter brackets that are slightly tipped up or down due to an uneven mounting surface will be naturally brought into line during the phase of attaching the gutter to the bracket if they are not tightened too tight. 3) As the raingutter expands and contracts, it is able to move the front end of the bracket where it is attached to the gutter.
Place the gutter in the brackets. The back portion of each bracket is inspected to see that the gutter is seated into the bracket hook. The bracket is held in a square and true position, and the gutter is held firmly into the bracket.
Further instructions for Moderne style gutter brackets only.
A 1/4” hole is drilled through the existing hole in the front of the bracket and through the gutter. Install the brass oval-head screw and locknut and washer.
Further instructions for ornate styles of gutter brackets only. (not Moderne styles)
The front bead of the gutter is pushed back just slightly to view the location of the screw hole in the front of the bracket. A sharply pointed scribe may be used to make a dimple in the outside face of the gutter directly over the small screw hole. A 1/4” hole is drilled through the front side of the gutter from the outside or from the inside of the gutter. The bracket is pushed enough to the side during drilling, to prevent drilling into the bracket.
If drilling from the inside of the gutter, use a small right angle drill and a 1/4” drill bit that has been ground down so that just 1/4” of drill bit extends from the chuck. Install the small stainless steel screw and brass washer from the inside of the gutter using a stubby screwdriver.
Further instructions for all gutter brackets.
When viewed up close, the installed gutter rarely contacts the gutter bracket along the entire inside bracket surface. These gaps are usually unnoticeable from normal viewing angles (and as the copper ages). If any such gap is bothersome, then carefully fill the gap with a small bead of dark brown silicone rubber.
Once the bracket and raingutter has been installed, if a bracket still looks a little crooked, then tip the bottom of the bracket to the left or right to improve the appearance.
Dings
During the placement of the gutter into the brackets and at other times, small dings may occur. Even large dings are often not noticeable once the gutter has patinaed, but on bright reflective copper even the smallest ding stands out when viewed from a distance. This can cause the client concern that is often seen to be unjustified as the copper ages, but is business problem non-the-less, because payments often need to be received while the material is still shiny. Dings can be reduced, if not eliminated, by massaging the gutter from the inside with the blunt plastic handle of a stubby screwdriver, or some similar device. Also the copper surface can be buffed with scotchbrite (tm) to reduce reflectivity.
Gutter Seams
A long lasting material such as copper should always get the best quality seam, which is one that has been riveted and soldered.
Hide the gutter seams behind the gutter brackets through a little advance planning. Overlap 2 lengths of gutter 1 inch at seams. Use CB42D rivets spaced on 1&1/2 inch centers. The seam should be soldered immediately upon installation of the rivets in order to prevent elongation of the rivet holes due to thermal expansion and contraction of the gutter. Care should be taken to see that the solder penetrates to the center of the rivet. Rinse the seam with water after soldering. Spray a stream of fresh water into the outside of the gutter seam. After plating and rinsing, a little high quality caulking might be placed where solder was not possible to access.
Copper Rivets
A copper rivet should not contain mild steel in the rivet or in the pin. Watch out for copper plated steel rivets or copper plated steel pins. If any part of the rivet sticks to a magnet, then the steel will expand and cause a leak or stain the copper. See Copperworks catalog for sources.
Gutter Miters
The cleanest looking gutter miter is cut into the stock material itself, using a gutter miter pattern. Leave a raw edge on one piece of gutter, and 3/4” tabs on the other piece of gutter. The overlap of the tabs should be cut so that they lay opposite to the way that the shingles of a roof would overlap, so that the solder will flow down into the seam easily. Approximately every third tab is riveted. The seam is soldered from the inside. Soldering starts with the upper vertical areas of the seam, and progresses down to the easier flat areas.
Prefabricated gutter miters are not recommended, but might be used if they meet the following qualifications.
1) The shape, size, and profile of the miter match that of the raingutter while the gutter sits in the gutter brackets being used.
2) Gutter brackets may hide the two gutter to miter seams on the prefabricated miter.
3) The factory seam in the middle of the miter must be soldered, and no other type of sealant should be used other than solder.
Roof-To-Wall Flashing
Most often, at locations where the end of a gutter butts into a wall, there should be a special roof-to-wall flashing. This flashing should pitch downward a little so that water will not drip back along its underside. Lay a bead of sealant along the top edge between the gutter end and the wall, and anywhere else that water might leak in this vulnerable area.
Gutter Mitered End Caps
A Return End is another name for this item. Gutter ends that do not about a flat surface are complimented by the style and grace of a mitered end cap.
A 3 piece Gutter Mitered End Cap Pattern Set is used to produce these ends in the field or in the shop. The end of the gutter length to be mitered is cut without tabs using the double ended template. A mitered end is cut from a small piece of scrap gutter material using the appropriate right or left end cap pattern. 1/2” inch tabs are allowed on the end caps. The tabs are cut in such a way so that the overlaps face upward. The tabs on the tubular gutter bead of a traditional half-round gutter are cut 1/4” apart, and 3/8” deep, and are formed with needle-nose pliers.
The end cap is clamped in place with a small c-clamp type vise grip(tm) placed just under the front bead. Align the bottom of the gutter end, and clamp a visegrip(tm) to the flange at the back of the gutter.
The gutter bead is set into a tight fit with the tap of a hammer, and then soldered on the top side of the gutter bead, near the area marked 1 on the pattern set. The c-clamp visegrip(tm) is removed.
The pointed part of the mitered end at the bottom (location 2) is fluxed. A small chunk of solder is set into it, and the location is held in place with a screwdriver, and gets tack soldered in place. The back part of the seam gets tack soldered 3 and the back visegrip(tm) is removed.
All the tabs are set more flush at this point by tapping from the inside. Two more locations may be tacked at 4 and 5. The entire seam is then very well fluxed and soldered primarily from the inside.
When doing this soldering, as well as when soldering gutter miters, it is important that the solder flow all the way out to the outside edge, so that the seam may be sanded flush on the outside surface later.
The seam is sanded smooth on the outside of the gutter first with a 24 grit sanding disk, and then with a 120 grit disk, and is then copper plated.
Double-Bottomed Gutter
One method for dealing with a low area in the gutter is to solder a second bottom into it. This method is best employed with a gutter that already has a deep bottom. A 5 inch half round gutter for example, has rather little capacity in most situations, and may not be a good candidate for this operation.
Start with the gutter completely installed and soldered. Fill the gutter with water and wait for the water to stop draining from the downspout. With a grease pencil mark the edge of the water line. Drain the water by drilling one or more 1/4” holes the lowest area of the gutter.
Mark 6 inch increment lines lengthwise along the low area and assign each mark a letter or number. Measure the width of the water line marks at each 6 inch line and note these measurements. The pieces of second bottom are produced of flat sheet. It is easiest for both production and installation, to keep the pieces less than 4 feet. Allow each piece to overlap the next at least 1 inch. Allow a 1/2 inch flange along the edge of each piece.
The pieces get soldered into the gutter. It helps in soldering to tack each piece in place every 6 inches, and then to solder each alternate 6 inch gap, and then go back and solder the remaining 6 inch gaps.
Radius Raingutter
Locations with curved roofs should have truly curved raingutter. Not a gutter composed of small straight pieces soldered together. The human eye is very discerning to lack of perfection in curved surfaces.
Radius gutter is custom produced at Copperworks in generally from 4 to 10 foot lengths. Shorter lengths not only are easier to ship, but any inconsistency or miscalculation in radius is divided up in finer increments. On one end of each piece is provided an internal sleeve to slip to the inside of the next piece, for a flush outside surface.
Radius Gutter Template
Using a water level, draw a line around the curved fascia which will represent the level of the upper back edge of the radius gutter. Cut a large sheet of cardboard into 4 to 6 foot long strips. The strips should be about 3 times as wide as the space that the curve will cross over for the given length of cardboard (see illustration). Start at one end of the fascia or a specific location marked by a short vertical line on the fascia. Label the first piece of cardboard A. Meticulously cut and trim the cardboard until it matches the curved fascia as perfectly as possible. One corner of cardboard A should align on the first line made on the fascia. Make another short vertical line on the fascia at the other corner of the cardboard. At approximately the center of the first two lines on the fascia make another line. Take a second piece of cardboard and label it B, and align one corner with the middle mark of A. Trim B until it is perfect and make another mark on the fascia at the other corner of cardboard B. Label a third piece of cardboard C, and align it with the existing mark that is the far edge of A, and the center point of B. Label the other side of the mark C. Trim C
TO BE CONTINUED
http://www.rain-watersystems.com/
This site is backed by 26+ years experience and contains insider tricks for professionals and information for homeowners that can be found nowhere else. Visit my WEBSITE and " LIKE " us on Facebook to keep up on our products and activities.
My normal service range is from Santa Monica to San Diego but I have installed copper gutters and rainwater harvesting systems in California, Nevada, Utah, Hawaii and Rwanda.
I have a small but national customer base through my gutter products website @ www.abraingutters.com where I offer rare items such has handmade weather vanes and hand carved and custom family crests for gates cast in aluminum or bronze. Through my websites you can gain knowledge, order products, beautify your home or help grow your business.
My normal service range is from Santa Monica to San Diego but I have installed copper gutters and rainwater harvesting systems in California, Nevada, Utah, Hawaii and Rwanda.
I have a small but national customer base through my gutter products website @ www.abraingutters.com where I offer rare items such has handmade weather vanes and hand carved and custom family crests for gates cast in aluminum or bronze. Through my websites you can gain knowledge, order products, beautify your home or help grow your business.
Sunday, January 2, 2011
Soldering Situations
For most field soldering situations installing copper rain gutters I use a propane torch with 50/50 solder. Some will say this leaves burn marks but I say that doesn't matter after a few days. We have gotten proficient with sweating the soft solder through the joints in this manner. Key is a proper temp.
When the flame is too high the solder runs like water and the metal contorts. When it is too low there is a poor bond. I use a small propane canister with a flexible hose. The tank is small enough that I can keep it in my tool bag and if you have ever tried to iron solder three stories in the air in a high wind you'll know it is difficult at best. We do have the luxury of a warm climate here in Southern California so we do not deal with the expansion and contraction some installers do.
When the situation calls for iron soldering I usually am working at a bench producing rectangular soldered downspouts. In this situation I do use a traditional soldering iron. I keep powdered sal ammoniac to mix with water as I like a hot, cleaned, tinned iron. The only trick I can think of is that I tin the irons with a lead free solder that has a much higher melting point as this seems to keep them clean longer. I also remove the irons from the flame when not in use as carbon builds on the iron ( which is actually a chunk of shaped copper ).
People call me all the time with questions about copper gutters and soldering. I am hoping that by the public using this portion of my website to ask these questions I can share the information with everybody. I have nothing to lose my sharing my experience.
Description
This section is from the book "Practical Sheet And Plate Metal Work", by Evan A. Atkins. Also available from Amazon: Practical Sheet And Plate Metal Work.Chapter XXXV. Sheet Metal Joints
There are really only five ways in which the edges of sheet and plate metals can be fastened together - viz., by soldered, brazed, welded, grooved, and riveted joints. But whilst we are limited to the use of one or other of these forms of jointing, there are numerous modifications of them in practice.
The sketches of joints shown are enlarged somewhat, to better exhibit the layers of metal. (1) shows the ordinary lap-joint, as used in soldering together the edges of tinplate, zinc, or galvanised iron, the width of lap running from about 1/8 in. in thin tinplate up to ¼ in. in galvanised iron.
To make a soldered joint is not a very difficult matter; but there are a few things that want to be taken notice of if the job is to be carried out successfully. The fluxes (anything that is used to assist the flow of metals) used are various; but those commonly in use are "killed spirits," and ready-prepared soldering fluids. "Killed spirits," or "spirits of salts," as it called, takes a good deal of beating for all-round work, as by its use almost any metal can be soldered, with the exception, perhaps, of aluminium. It is prepared by dissolving as much scrap zinc as possible in hydrochloric acid, the resulting liquid being known chemically as a solution of chloride of zinc. If the edges of the metal are clean, they can be lapped over without any preparation, and the spirits applied along the joint with a brush about 1/8 in. wide - a good brush can be made with a few bristles fixed into a strip of double-over tinplate. Before using the soldering-bit it should be seen that it is
properly tinned, and if not, get to dark-red heat, file the point about | in. along, dip in spirits, and then apply solder.
The mistake that the novice usually makes in soldering a joint is to stick the metal on like glue or putty, instead of holding the soldering-iron long enough against the joint for the solder to be properly melted and the joint to get sufficiently hot for the solder and sheet metal to firmly adhere together. Instead of using the extreme point of
the soldering-iron to run the solder on joint, an edge of the square point should be used to draw along the solder. In this way a greater quantity of heat will be transmitted to the joint, and thus a better and quicker job made.
The soldering-iron must be watched, so that it does not get red-hot, or else the tinning on its point will be burnt off, or, what is worse, form a hard skin of bronze, which is somewhat difficult to file away. When the soldering-iron is drawn from the fire it can be cleaned by quickly dipping the point into the spirits, and also in this way one can judge as to its proper temperature. If when dipping the iron into the spirits much smoke is given off, or the liquid spurts about, the iron is too hot; or, on the other hand, if small bubbles of spirit adhere to the soldering-iron it is not hot enough. An hour's practice should teach one the proper temperature at which to use the bit.
In soldering zinc or galvanised iron, if the soldering-bit is too hot the joint will be very rough on account of some of the zinc being melted from the surface of sheet and mixing in the solder. For tarnished zinc and galvanised iron, the spirits should not be quite "dead," that is, the scrap zinc should be withdrawn from the acid before the boiling action has quite ceased. It is, perhaps, a better plan, though, to freshen up the "killed spirits" by adding a small quantity of neat acid.
In soldering copper, brass, and black iron, the edges of metal should be carefully cleaned before the lap is formed. One of the tests of a good soldered joint is that the solder shall have run right through the joint, and if this be done, and the joint properly cleaned with soda and water, there is little danger of corrosion from the use of chloride of zinc. The great drawback to the use of this flux is in the corroding action that takes place if any be left about the joint; perhaps the chief evil being when it is not properly driven out from between the laps with the running solder.
The sketches of joints shown are enlarged somewhat, to better exhibit the layers of metal. (1) shows the ordinary lap-joint, as used in soldering together the edges of tinplate, zinc, or galvanised iron, the width of lap running from about 1/8 in. in thin tinplate up to ¼ in. in galvanised iron.
To make a soldered joint is not a very difficult matter; but there are a few things that want to be taken notice of if the job is to be carried out successfully. The fluxes (anything that is used to assist the flow of metals) used are various; but those commonly in use are "killed spirits," and ready-prepared soldering fluids. "Killed spirits," or "spirits of salts," as it called, takes a good deal of beating for all-round work, as by its use almost any metal can be soldered, with the exception, perhaps, of aluminium. It is prepared by dissolving as much scrap zinc as possible in hydrochloric acid, the resulting liquid being known chemically as a solution of chloride of zinc. If the edges of the metal are clean, they can be lapped over without any preparation, and the spirits applied along the joint with a brush about 1/8 in. wide - a good brush can be made with a few bristles fixed into a strip of double-over tinplate. Before using the soldering-bit it should be seen that it is
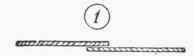


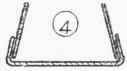





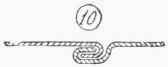


The mistake that the novice usually makes in soldering a joint is to stick the metal on like glue or putty, instead of holding the soldering-iron long enough against the joint for the solder to be properly melted and the joint to get sufficiently hot for the solder and sheet metal to firmly adhere together. Instead of using the extreme point of


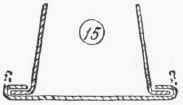


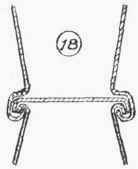

The soldering-iron must be watched, so that it does not get red-hot, or else the tinning on its point will be burnt off, or, what is worse, form a hard skin of bronze, which is somewhat difficult to file away. When the soldering-iron is drawn from the fire it can be cleaned by quickly dipping the point into the spirits, and also in this way one can judge as to its proper temperature. If when dipping the iron into the spirits much smoke is given off, or the liquid spurts about, the iron is too hot; or, on the other hand, if small bubbles of spirit adhere to the soldering-iron it is not hot enough. An hour's practice should teach one the proper temperature at which to use the bit.

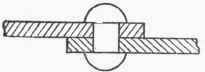


In soldering copper, brass, and black iron, the edges of metal should be carefully cleaned before the lap is formed. One of the tests of a good soldered joint is that the solder shall have run right through the joint, and if this be done, and the joint properly cleaned with soda and water, there is little danger of corrosion from the use of chloride of zinc. The great drawback to the use of this flux is in the corroding action that takes place if any be left about the joint; perhaps the chief evil being when it is not properly driven out from between the laps with the running solder.
Installation Instructions for the Do-It-Yerselfer
( NOTE: for step by step instructions with pictures click here. )
Installation of the Gutter Sections
WARNING: Copper is a sharp metal and will bite you if you let it. Firmly and securely, hold all pieces when working with them. Do not slide your hands or fingers along any straight or finished edges. This is partly the reason why we wore gloves in our demonstration. Wearing gloves will also help minimize the fingerprint marks on the gutter system. The best gloves to use especially for grip are ones with the palm and fingers coated with a rubber or latex material.
Tools Required:
Tape Measure
Metal Scribe
Cutting Tools (this could consist of combination of many things here are a few)
Green and/or Red Tin Snips also Know as Left and Right Handed Tin Snips Respectively
Hack Saw with new blade preferably
Miter Box is handy for straighter cuts
Compound Miter Saw with either
Solid Carbide Metal Cutting Blade (get it at two words W_l M_r_) this blade leaves burrs, so you will need a utility knife with a curved or “Hook Blade” as it’s known to help scrape off the burrs
Slate and Copper’s Anything Cutting Blade (gives you that factory cut every time, effortlessly).
Cord or Cordless Drill (3/8” size drill is perfect)
1/8” Drill Bit for Drill
Pop Rivet Gun
1/8” Diameter Copper Rivets
*Slate and Copper offers two sizes of Copper Rivets, 1/8”diameter by 1/8” tall, or 1/8” diameter by 1/4” tall. If you do not use Slate and Copper’s Copper Rivets with Solid Brass Pins (Mandrels), then make sure the copper rivets you do use have a solid copper, bronze, or brass pins, and not a copper, bronze, or brass coated steel pins. If you do use copper rivets with the steel coated pins, then the pins will eventually rust out and can potentially cause leaks depending on where the rivets are used.
C Clamps (optional but very useful)
Soldering Equipment and Flux (do not use the pre-tinning flux)
Soldering Iron of some sort (many styles to choose from)
Propane (blue tank) with an Adjustable Flame Torch Head Nozzle
First step; we must determine the length of the run, and cut the gutter to length. For runs greater than a 10' or 18' length of gutter we need to cut and join two or more pieces of gutter together. When cutting gutter to make a longer run we also need to determine what the overlap of the gutter will be, and take this into consideration before we cut the gutter sections to length. The minimum overlap of gutter into gutter should be 3/4”, max overlap is what ever you want it to be. We suggest that 1 1/2” overlap is perfect. When overlapping gutters to make longer runs keep in mind the way the water will flow, and/or if the gutter is being pitched to one end or the other. Why? Because to help with water drainage we want to overlap the higher gutter into the lower gutter, or in the direction of the flow of water toward the outlet.
Example, if we have a 25' - 3 1/2" (303.5") straight run that slopes from left to right, the outlet being on the right end. We can use 3 - 10' gutter sections, but remember when using 10' gutter sections they are actually 118 3/16" long, and not 120" long. To make it easy on ourselves we can basically forget about the 3/16" dimension, or use that as a little bit more on the overlap. Each gutter section at 118" equals 354" total without any overlap, and we need 303.5" of that. We take 303.5" minus 118" = 185.5 minus 118" = 67.5" now we take 67.5" and add 3" = 70.5". Why are we adding 3" to the 67.5" dimension? Because we have two overlapping seams, and each seam we want to overlap 1 1/2" each = 3" of total overlap. The 70.5" is the dimension we need to cut one of our 10' gutter sections to. If we take 118" + 118" +70.5" we get 306.5" minus 3" for the total overlap gives us our 303.5" or 25' - 3 1/2" gutter section. We want to overlap the far left 118" gutter section inside of the other 118" gutter section, and the middle piece of gutter (the other 118" section) gets overlapped into the 70.5" gutter section on the end. You can use the short section anywhere you want, as the far left piece, as the middle piece, or as the far right piece. As long as you overlap the gutter sections into each other correctly it really doesn't matter where you use the short section. If you really wanted to you could cut each of the gutter sections equally so they were all the same. I dare you to do that math.
( the picture numbers below are out of date but the descriptions are good )
Second step; once we have our measurements, and we have cut the gutter sections to length we can install the gutter sections together to make our longer run. Picture PB194313 shows all the tools necessary to install our two copper gutter sections together. The picture below PB194313 is Vice Grip “C” Clamps another useful tool for gutter installation, and later we will learn how useful they really are. First we need to determine the overlap, and for this installation demonstration we are using 1 1/2” overlap. In pictures PB194314, PB194316, & PB194317 we are marking the gutter with a metal scribe. You want to make at least 3 marks on the gutter just like the previous mentioned pictures show. Why you ask? The one on the front bead is going to help us line up better when we overlap at the bead, and the other two are also strategically located as well. After making the marks we need to bend up the back overflow lip on the back of the gutter up slightly. Why? Because if we don’t when we do go to overlap the gutter sections into each other the one overflow lip on the unbent gutter will not slip up under the back overflow lip on the other piece of gutter. If you don’t have, want to buy, or rent hand breaks another method is to take a pair of tin snips and cut right on the mark we made on the back lip all the way to the top of the back lip. In pictures PB194319 & PB194320 we used a pair of 2” hand breaks right on the mark to bend the back lip up slightly. Notice in picture PB194320 we only needed to bend the back lip up this far, and picture PB194321 is the result of the bend. Now we take and line the gutter sections up like in picture PB194322. In picture PB194322 The gutter section on the left is going to be overlapped into the gutter section on the right. In picture PB194323 we rotate at the bead the gutter section on the left until we are able to slide the two front beads into each other. Once we are overlapped at the bead we want to line the gutter section on the left up to the mark we made on the top of the front of the bead of the gutter we are overlapping into. Once lined up at the bead we can rotate the gutter down inside of the other gutter section and lock the back lips together (see pictures PB194324 & PB194325). Make sure you are lined up on all our marks, and make any adjustments if necessary. Now we can rivet the gutter sections together to hold them into position for soldering. In picture PB194326 we are showing the area (in-between the fingers) where we want to install the rivet on the front bead of the gutter. By putting the rivet here we are concealing the rivet so it will never be seen. Pictures PB194327, PB194328, and PB194329 we are installing the rivet in the front bead. In Picture PB194330 we are showing the underside of the gutter with just the one rivet installed, and if you notice we have a gap on the underside seam. We want to get rid of this gap before we drill for the other rivet on the back of the gutter. We take a pair of “C” clamps and first clamp onto the front of the gutter like picture PB194331 shows. Notice in picture PB194332 how we got rid of the gap on the front of the gutter just by using the one clamp. Picture PB194333 shows by just using one clamp on the front now the back of the gutter is lower. This means our gutter has a tight fitting seam. In picture PB194334 we used another clamp on the back of the gutter. In pictures PB194335, PB194336, PB194337, & PB194338 we installed the rivet on the back of the gutter. If we really wanted too we can take our hand breaks and bend the back overflow lip so it looks a little nicer as picture PB194339 is showing. Picture PB194340 shows the underside seam of the gutter section we just riveted together. Now the only thing left to do is to solder the gutter section together to make it watertight, and also to make the seam stronger.
Third step; flux and solder the gutter section seams together. For our soldering installation demonstration we used a 3” overlap. No real reason why but just to do a 3” overlap, and we didn't use the "C" clamps. Picture PB144270 we are applying flux with a flux brush all the way around the inside of the gutter. We must apply flux to our seam, or the solder will not stick to the copper at all. If flux is not applied or gets dried out during soldering, then the solder will bead off like mercury. Simply apply or reapply some flux. Pictures PB144271 through PB144278 we are soldering the copper gutter seam. If you are using a hand held torch to solder, then you will not need as many tack solder points 4 to 5 would do. Since we used a soldering iron as you can see in picture PB144272 we made many tack solder points. This many tack points is going to make our soldering job easier. In picture PB144271 a helpful hand was used to compress the metal together to get rid of a gap in the seam just until the craftsman who is soldering could tack solder that area. In pictures PB144273 & PB144274 the craftsman is building up and filling in-between his tack points with solder. When soldering copper gutter seams you will typically used more solder. Why? Because we want to make sure our soldered seam never leaks. It will end up helping us in the long run because with expansion contraction over time this type of seam will outperform any sweated type seam for sure. If you take notice in pictures PB144274 & PB144277 the craftsman is melting the solder with the tip of his soldering iron, and pulling the solder from the low side to the high side. By doing this his is actually pulling or drawing the solder into the overlapped seam. This is why the solder path is wider than any of the other solder seams you may have seen and/or read about in other parts of our installation manual. Solder will always flow to the highest temperature, and with the tip of the soldering iron being hotter than the surrounding copper the solder is sucked into the seam by doing this motion. Notice in picture PB144278 the drag lines from the tip of the soldering iron, and also please note the clean, beautiful, and perfectly completed soldering job on the inside of the gutter. There should be no solder that bleed through on the underside of the gutter. That absence of solder is just what we are looking for. This means we did a good job. If you would to learn more about soldering and the types of tools required seee my expert installation guide.
Common questions asked about copper and copper gutter:
Do I solder on the inside or the outside of the copper gutter, or both? Soldering is generally always done on the inside of the copper gutter. There would be no real advantage to do the soldering on the outside, or even both sides. If you did decide to solder on both sides, then you would have a pretty darn strong seam. If you really wanted a stronger seam, then you could simply put 4 or 5 rivets in the seam before soldering, and that would make it stronger too, heck there’s already 2 in it now. Putting 5, 6, or even 7 rivets in the overlapped gutter seams would be recommended on runs greater than 50’ in length, and especially if you are using 10’ gutter sections.
Will leaving the flux on the copper gutter system harm or discolor the copper? No and Yes, no to the first part, and yes to the second. Leaving most common fluxes on the gutter will actually turn green usually within a week or two. As long as you don't smear flux all over the outside of the gutter, or anywhere visible on the system you will be fine. If flux turning green is a concern, then simply do as we did after we were done soldering and use a clean rag and wipe it off. You can get rid of any chance of the flux turning green by washing and rinsing the area where flux was applied with mildly soapy water.
How much slope or pitch do I need when hanging the gutter? Any gutter can be hung level, and it will drain water. Water can only fill up so far in a gutter before it finds an outlet, and from there gravity and physics takes over pulling the water toward the outlet or hole in the bottom of the gutter anyway. For better drainage a gutter can be pitched 1/8" per every 10' of gutter length. Gutter does not need to be pitched any more than this, but certainly can be if so desired.
How long does a copper gutter system last? A 16 ounce copper gutter system will generally last about 75 years or so. This time can be shortened depending on environment and even roofing material. If the roofing material is asphalt shingles, then a 16 ounce gutter system may only last about 45 - 55 years or so. Why? Because the grains coming off of the shingles act as sandpaper over time wearing down the copper. How long will 20 ounce copper gutter last? A 20 ounce gutter system will service about a century or longer, and this life expectancy can be shortened depending on the roofing material used and the environment as well.
Why does copper turn colors? Copper will always turn different shades and colors because copper is exposed to the oxygen in the atmosphere. A.B Raingutters does sell products which protect the copper from turning brown. These products all last for about 10 to 12 years or so. Then the product needs to be re-applied, or you can let the copper go its natural course. One such product is called Incralac. Typically, in a normal environment, copper will turn from a shiny new penny look to fazes of turning brown, then eventually dark brown within a couple of months to a year or so. Then copper will turn to a streaking green, then to a darker greenish color. This may not happen for 30 to 50 years give or take a decade or two. Then copper will turn to a blue-green color 50 to 100 years down the road. If you have ever see copper that is green or blue-green it is more than likely old copper. When copper gets to the end of its life it will usually be in its blue-green stage, and there will be streaks of copper or orange color coming back through the blue-green patina. Patina products are available as well to turn the copper gutter system to a green/blue-green color.
Slideshow
Installation of the Gutter Sections
WARNING: Copper is a sharp metal and will bite you if you let it. Firmly and securely, hold all pieces when working with them. Do not slide your hands or fingers along any straight or finished edges. This is partly the reason why we wore gloves in our demonstration. Wearing gloves will also help minimize the fingerprint marks on the gutter system. The best gloves to use especially for grip are ones with the palm and fingers coated with a rubber or latex material.
Tools Required:
Tape Measure
Metal Scribe
Cutting Tools (this could consist of combination of many things here are a few)
Green and/or Red Tin Snips also Know as Left and Right Handed Tin Snips Respectively
Hack Saw with new blade preferably
Miter Box is handy for straighter cuts
Compound Miter Saw with either
Solid Carbide Metal Cutting Blade (get it at two words W_l M_r_) this blade leaves burrs, so you will need a utility knife with a curved or “Hook Blade” as it’s known to help scrape off the burrs
Slate and Copper’s Anything Cutting Blade (gives you that factory cut every time, effortlessly).
Cord or Cordless Drill (3/8” size drill is perfect)
1/8” Drill Bit for Drill
Pop Rivet Gun
1/8” Diameter Copper Rivets
*Slate and Copper offers two sizes of Copper Rivets, 1/8”diameter by 1/8” tall, or 1/8” diameter by 1/4” tall. If you do not use Slate and Copper’s Copper Rivets with Solid Brass Pins (Mandrels), then make sure the copper rivets you do use have a solid copper, bronze, or brass pins, and not a copper, bronze, or brass coated steel pins. If you do use copper rivets with the steel coated pins, then the pins will eventually rust out and can potentially cause leaks depending on where the rivets are used.
C Clamps (optional but very useful)
Soldering Equipment and Flux (do not use the pre-tinning flux)
Soldering Iron of some sort (many styles to choose from)
Propane (blue tank) with an Adjustable Flame Torch Head Nozzle
First step; we must determine the length of the run, and cut the gutter to length. For runs greater than a 10' or 18' length of gutter we need to cut and join two or more pieces of gutter together. When cutting gutter to make a longer run we also need to determine what the overlap of the gutter will be, and take this into consideration before we cut the gutter sections to length. The minimum overlap of gutter into gutter should be 3/4”, max overlap is what ever you want it to be. We suggest that 1 1/2” overlap is perfect. When overlapping gutters to make longer runs keep in mind the way the water will flow, and/or if the gutter is being pitched to one end or the other. Why? Because to help with water drainage we want to overlap the higher gutter into the lower gutter, or in the direction of the flow of water toward the outlet.
Example, if we have a 25' - 3 1/2" (303.5") straight run that slopes from left to right, the outlet being on the right end. We can use 3 - 10' gutter sections, but remember when using 10' gutter sections they are actually 118 3/16" long, and not 120" long. To make it easy on ourselves we can basically forget about the 3/16" dimension, or use that as a little bit more on the overlap. Each gutter section at 118" equals 354" total without any overlap, and we need 303.5" of that. We take 303.5" minus 118" = 185.5 minus 118" = 67.5" now we take 67.5" and add 3" = 70.5". Why are we adding 3" to the 67.5" dimension? Because we have two overlapping seams, and each seam we want to overlap 1 1/2" each = 3" of total overlap. The 70.5" is the dimension we need to cut one of our 10' gutter sections to. If we take 118" + 118" +70.5" we get 306.5" minus 3" for the total overlap gives us our 303.5" or 25' - 3 1/2" gutter section. We want to overlap the far left 118" gutter section inside of the other 118" gutter section, and the middle piece of gutter (the other 118" section) gets overlapped into the 70.5" gutter section on the end. You can use the short section anywhere you want, as the far left piece, as the middle piece, or as the far right piece. As long as you overlap the gutter sections into each other correctly it really doesn't matter where you use the short section. If you really wanted to you could cut each of the gutter sections equally so they were all the same. I dare you to do that math.
( the picture numbers below are out of date but the descriptions are good )
Second step; once we have our measurements, and we have cut the gutter sections to length we can install the gutter sections together to make our longer run. Picture PB194313 shows all the tools necessary to install our two copper gutter sections together. The picture below PB194313 is Vice Grip “C” Clamps another useful tool for gutter installation, and later we will learn how useful they really are. First we need to determine the overlap, and for this installation demonstration we are using 1 1/2” overlap. In pictures PB194314, PB194316, & PB194317 we are marking the gutter with a metal scribe. You want to make at least 3 marks on the gutter just like the previous mentioned pictures show. Why you ask? The one on the front bead is going to help us line up better when we overlap at the bead, and the other two are also strategically located as well. After making the marks we need to bend up the back overflow lip on the back of the gutter up slightly. Why? Because if we don’t when we do go to overlap the gutter sections into each other the one overflow lip on the unbent gutter will not slip up under the back overflow lip on the other piece of gutter. If you don’t have, want to buy, or rent hand breaks another method is to take a pair of tin snips and cut right on the mark we made on the back lip all the way to the top of the back lip. In pictures PB194319 & PB194320 we used a pair of 2” hand breaks right on the mark to bend the back lip up slightly. Notice in picture PB194320 we only needed to bend the back lip up this far, and picture PB194321 is the result of the bend. Now we take and line the gutter sections up like in picture PB194322. In picture PB194322 The gutter section on the left is going to be overlapped into the gutter section on the right. In picture PB194323 we rotate at the bead the gutter section on the left until we are able to slide the two front beads into each other. Once we are overlapped at the bead we want to line the gutter section on the left up to the mark we made on the top of the front of the bead of the gutter we are overlapping into. Once lined up at the bead we can rotate the gutter down inside of the other gutter section and lock the back lips together (see pictures PB194324 & PB194325). Make sure you are lined up on all our marks, and make any adjustments if necessary. Now we can rivet the gutter sections together to hold them into position for soldering. In picture PB194326 we are showing the area (in-between the fingers) where we want to install the rivet on the front bead of the gutter. By putting the rivet here we are concealing the rivet so it will never be seen. Pictures PB194327, PB194328, and PB194329 we are installing the rivet in the front bead. In Picture PB194330 we are showing the underside of the gutter with just the one rivet installed, and if you notice we have a gap on the underside seam. We want to get rid of this gap before we drill for the other rivet on the back of the gutter. We take a pair of “C” clamps and first clamp onto the front of the gutter like picture PB194331 shows. Notice in picture PB194332 how we got rid of the gap on the front of the gutter just by using the one clamp. Picture PB194333 shows by just using one clamp on the front now the back of the gutter is lower. This means our gutter has a tight fitting seam. In picture PB194334 we used another clamp on the back of the gutter. In pictures PB194335, PB194336, PB194337, & PB194338 we installed the rivet on the back of the gutter. If we really wanted too we can take our hand breaks and bend the back overflow lip so it looks a little nicer as picture PB194339 is showing. Picture PB194340 shows the underside seam of the gutter section we just riveted together. Now the only thing left to do is to solder the gutter section together to make it watertight, and also to make the seam stronger.
Third step; flux and solder the gutter section seams together. For our soldering installation demonstration we used a 3” overlap. No real reason why but just to do a 3” overlap, and we didn't use the "C" clamps. Picture PB144270 we are applying flux with a flux brush all the way around the inside of the gutter. We must apply flux to our seam, or the solder will not stick to the copper at all. If flux is not applied or gets dried out during soldering, then the solder will bead off like mercury. Simply apply or reapply some flux. Pictures PB144271 through PB144278 we are soldering the copper gutter seam. If you are using a hand held torch to solder, then you will not need as many tack solder points 4 to 5 would do. Since we used a soldering iron as you can see in picture PB144272 we made many tack solder points. This many tack points is going to make our soldering job easier. In picture PB144271 a helpful hand was used to compress the metal together to get rid of a gap in the seam just until the craftsman who is soldering could tack solder that area. In pictures PB144273 & PB144274 the craftsman is building up and filling in-between his tack points with solder. When soldering copper gutter seams you will typically used more solder. Why? Because we want to make sure our soldered seam never leaks. It will end up helping us in the long run because with expansion contraction over time this type of seam will outperform any sweated type seam for sure. If you take notice in pictures PB144274 & PB144277 the craftsman is melting the solder with the tip of his soldering iron, and pulling the solder from the low side to the high side. By doing this his is actually pulling or drawing the solder into the overlapped seam. This is why the solder path is wider than any of the other solder seams you may have seen and/or read about in other parts of our installation manual. Solder will always flow to the highest temperature, and with the tip of the soldering iron being hotter than the surrounding copper the solder is sucked into the seam by doing this motion. Notice in picture PB144278 the drag lines from the tip of the soldering iron, and also please note the clean, beautiful, and perfectly completed soldering job on the inside of the gutter. There should be no solder that bleed through on the underside of the gutter. That absence of solder is just what we are looking for. This means we did a good job. If you would to learn more about soldering and the types of tools required seee my expert installation guide.
Common questions asked about copper and copper gutter:
Do I solder on the inside or the outside of the copper gutter, or both? Soldering is generally always done on the inside of the copper gutter. There would be no real advantage to do the soldering on the outside, or even both sides. If you did decide to solder on both sides, then you would have a pretty darn strong seam. If you really wanted a stronger seam, then you could simply put 4 or 5 rivets in the seam before soldering, and that would make it stronger too, heck there’s already 2 in it now. Putting 5, 6, or even 7 rivets in the overlapped gutter seams would be recommended on runs greater than 50’ in length, and especially if you are using 10’ gutter sections.
Will leaving the flux on the copper gutter system harm or discolor the copper? No and Yes, no to the first part, and yes to the second. Leaving most common fluxes on the gutter will actually turn green usually within a week or two. As long as you don't smear flux all over the outside of the gutter, or anywhere visible on the system you will be fine. If flux turning green is a concern, then simply do as we did after we were done soldering and use a clean rag and wipe it off. You can get rid of any chance of the flux turning green by washing and rinsing the area where flux was applied with mildly soapy water.
How much slope or pitch do I need when hanging the gutter? Any gutter can be hung level, and it will drain water. Water can only fill up so far in a gutter before it finds an outlet, and from there gravity and physics takes over pulling the water toward the outlet or hole in the bottom of the gutter anyway. For better drainage a gutter can be pitched 1/8" per every 10' of gutter length. Gutter does not need to be pitched any more than this, but certainly can be if so desired.
How long does a copper gutter system last? A 16 ounce copper gutter system will generally last about 75 years or so. This time can be shortened depending on environment and even roofing material. If the roofing material is asphalt shingles, then a 16 ounce gutter system may only last about 45 - 55 years or so. Why? Because the grains coming off of the shingles act as sandpaper over time wearing down the copper. How long will 20 ounce copper gutter last? A 20 ounce gutter system will service about a century or longer, and this life expectancy can be shortened depending on the roofing material used and the environment as well.
Why does copper turn colors? Copper will always turn different shades and colors because copper is exposed to the oxygen in the atmosphere. A.B Raingutters does sell products which protect the copper from turning brown. These products all last for about 10 to 12 years or so. Then the product needs to be re-applied, or you can let the copper go its natural course. One such product is called Incralac. Typically, in a normal environment, copper will turn from a shiny new penny look to fazes of turning brown, then eventually dark brown within a couple of months to a year or so. Then copper will turn to a streaking green, then to a darker greenish color. This may not happen for 30 to 50 years give or take a decade or two. Then copper will turn to a blue-green color 50 to 100 years down the road. If you have ever see copper that is green or blue-green it is more than likely old copper. When copper gets to the end of its life it will usually be in its blue-green stage, and there will be streaks of copper or orange color coming back through the blue-green patina. Patina products are available as well to turn the copper gutter system to a green/blue-green color.
Slideshow
Rain Water Harvesting
Links listed here will help provide knowledge about rain water harvesting.
I am pleased to be amongst the leaders of Rain Water Harvesting in Southern California. Please take a moment and review part of my portfolio of completed projects.
Check it out here.
Please view The Cycle of Insanity video. When I show people this video and explain how much water they can collect their jaws drop. The way we manage our resources is insane. Harvesting rainwater is an easy and realistic way to conserve water in Los Angeles. There is plenty of rain. If one thousand feet of roof area were collected in Los Angeles that would yield 8,700 gallons per year with our average of 14" per year.
Rain water harvesting combined with grey water systems and Xeriscape Gardening can reduce outdoor watering to zero.
TO SEE THE AVERAGE YEARLY RAINFALL IN YOUR CALIFORNIA CITY, CLICK HERE.
Number geeks and grid techs may enjoy this, but when I meet with a client the first thing I ascertain is how much space they have for above ground storage. Below ground is an option, but generally costs triple and involves permits from the government. Sometimes we can capture waste water from the clothes washer or water filters ( gray water ) and run that into the same cisterns that collect the rainwater and run a line back into the house to power a toilet.
One of those questions we must ask ourselves is why are we flushing human waste down the drain with potable water?
You can easily find a water tank on the web today made for agricultural or commercial customers. These tanks are generally too large for residential use and typically come in black, white and dark green. Bushman specializes in slimline tanks that fit under the eaves of the house and come in over six color choices.
Alternatively you can pick-up a rain barrel at the local nursery. While these may look great under a downpipe in your garden, they typically store no more than 60 gallons, which is inadequate for most garden sizes. We recommend a minimum of 300 gallons of storage, purpose built to collect and store clean rainwater. Also beware of recycling old plastic containers to rain barrels as they may have been used to transport harsh chemicals for their original purpose and could leech poorer quality plastic.
Because of contamination on the roof the first volume of rain should be diverted from the storage tank.
Detailed information on First Flush Devices can be found here.
I am pleased to be amongst the leaders of Rain Water Harvesting in Southern California. Please take a moment and review part of my portfolio of completed projects.
Check it out here.
Please view The Cycle of Insanity video. When I show people this video and explain how much water they can collect their jaws drop. The way we manage our resources is insane. Harvesting rainwater is an easy and realistic way to conserve water in Los Angeles. There is plenty of rain. If one thousand feet of roof area were collected in Los Angeles that would yield 8,700 gallons per year with our average of 14" per year.
Rain water harvesting combined with grey water systems and Xeriscape Gardening can reduce outdoor watering to zero.
TO SEE THE AVERAGE YEARLY RAINFALL IN YOUR CALIFORNIA CITY, CLICK HERE.
Number geeks and grid techs may enjoy this, but when I meet with a client the first thing I ascertain is how much space they have for above ground storage. Below ground is an option, but generally costs triple and involves permits from the government. Sometimes we can capture waste water from the clothes washer or water filters ( gray water ) and run that into the same cisterns that collect the rainwater and run a line back into the house to power a toilet.
One of those questions we must ask ourselves is why are we flushing human waste down the drain with potable water?
Drought
Many parts of the United States are in (or are about to enter) a drought period, facing possible water restrictions. The government will use the excuse of a drought, real or imagined, to raise your water rates. In February 2009, the Governor of California ordered that mandatory water rationing and mandatory reductions in water use may be introduced. Governor Schwarzenegger called for a statewide water reduction of 20%. I suspect that even after the record snows and rains of 2010-2011 the buzz will be that there is a drought. If you take the time to watch the video above you will see that the real problem is lack of planning and knowledge about water conservation.
One of the things you can do is STOP PAYING THEM FOR WATER THAT YOU OWN, THAT FLOWS OFF YOUR PROPERTY.
Rain tanks, or rain barrels, collect fresh rain water from the home roof and store it for times of drought. Modern rain tanks are sealed from light, animals and vegetable matter so the water stays clean for months.
Proponents of global warming warn that weather patterns are already changing and traditional rainfall levels are expected to drop in many areas.
One of the things you can do is STOP PAYING THEM FOR WATER THAT YOU OWN, THAT FLOWS OFF YOUR PROPERTY.
Rain tanks, or rain barrels, collect fresh rain water from the home roof and store it for times of drought. Modern rain tanks are sealed from light, animals and vegetable matter so the water stays clean for months.
Proponents of global warming warn that weather patterns are already changing and traditional rainfall levels are expected to drop in many areas.
Green Living
Green living is now becoming a way of life for a majority of Americans. People are conscious of their 'carbon footprint' and are seeking methods to reduce the future impact on the environment and climate. 20% of California's power consumption is used to collect, transport and treat water.
In areas of major urbanization the environment is suffering from increased run-off that cannot soak naturally into the ground. As a result, aquifers are not filling at a rate fast enough to restore their pre-urban levels.
In areas of major urbanization the environment is suffering from increased run-off that cannot soak naturally into the ground. As a result, aquifers are not filling at a rate fast enough to restore their pre-urban levels.
Saving Clean Water For Drinking
Water is a limited resource and the cost of its supply is certain to rise in the next few years. Most major water collection and distribution projects in California were completed over fifty years ago and no new major rainwater catchment projects are planned. Water restrictions are nothing new in California, but since the last major drought in the early 1990s, the state's population has grown by 9 million to a total of 38 million. In a press conference on March 12, 2009 the governor plainly stated that, with increased demand and limited supply, Californians can expect to pay more for water in the future.
But why use good drinking water on the garden or to flush toilets? Over 40% of water supplied to most suburban households is used on the garden. This is not the best use of a product processed for human consumption. Besides, most plants enjoy the slightly acidic and soft qualities of rainwater.
Bushman rainwater harvesting tanks maintain a high quality of rain water with gutter guards, insect filters and first flush devices that divert the first rains of the season to the drain. All tanks are opaque and do not allow the growth of algae. Tanks are made or lined with food grade quality polyethylene.
But why use good drinking water on the garden or to flush toilets? Over 40% of water supplied to most suburban households is used on the garden. This is not the best use of a product processed for human consumption. Besides, most plants enjoy the slightly acidic and soft qualities of rainwater.
Bushman rainwater harvesting tanks maintain a high quality of rain water with gutter guards, insect filters and first flush devices that divert the first rains of the season to the drain. All tanks are opaque and do not allow the growth of algae. Tanks are made or lined with food grade quality polyethylene.
Design
You can easily find a water tank on the web today made for agricultural or commercial customers. These tanks are generally too large for residential use and typically come in black, white and dark green. Bushman specializes in slimline tanks that fit under the eaves of the house and come in over six color choices.
Alternatively you can pick-up a rain barrel at the local nursery. While these may look great under a downpipe in your garden, they typically store no more than 60 gallons, which is inadequate for most garden sizes. We recommend a minimum of 300 gallons of storage, purpose built to collect and store clean rainwater. Also beware of recycling old plastic containers to rain barrels as they may have been used to transport harsh chemicals for their original purpose and could leech poorer quality plastic.
Because of contamination on the roof the first volume of rain should be diverted from the storage tank.
Detailed information on First Flush Devices can be found here.
Company History
Way back when, in the 1970's there was a little company in Salt Lake City called K.R. Kennedy Raingutters. Some say Rain Gutters, but pops said Raingutters and so it has always been for me. Kurt Kennedy also did painting and designed implements for the sewing and knitting industry. Those who knew him may be surprised to know he held patents. He was not educated, but he was wise. Rest in peace Kurt.
I am now partnered with Classic Gutters, LLC as an independent West coast branch and my installation company is called Rain Water Systems.
We do all types of gutters: crazy high end copper, regualr aluminum, and we are a leader in Rain Water Harvesting applications.
Subscribe to:
Posts (Atom)